In the intricate world of automotive production, the brake drum manufacturing process stands as a testament to engineering precision and innovation. Renowned for their simplicity and cost-effectiveness, brake drums play a vital role in vehicle braking systems, primarily in heavy-duty trucks and older model cars. The process of manufacturing these components not only requires advanced technical expertise but also demands adherence to rigorous quality standards. This article delves into the distinct stages of brake drum manufacturing, highlighting best practices and technological innovations that set the standards for excellence.
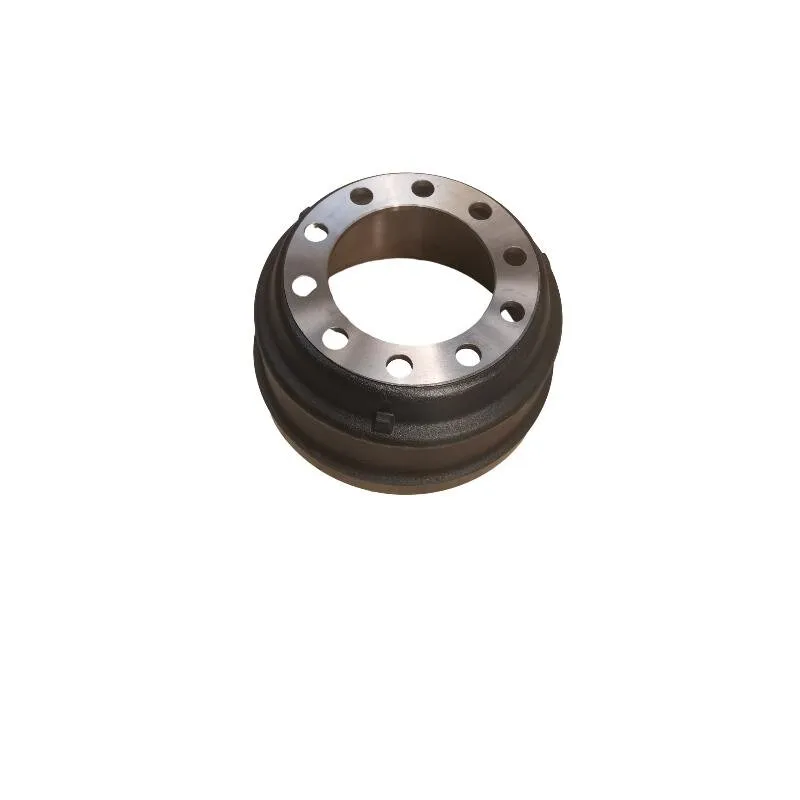
Brake drum production commences with the selection of appropriate raw materials. Typically, cast iron is the material of choice due to its optimal properties of strength, wear resistance, and thermal conductivity. The high carbon content in cast iron enhances its ability to dissipate heat generated from friction, a critical requirement for efficient braking. Ensuring the purity and quality of cast iron is paramount as impurities can significantly compromise the structural integrity and performance of the final product.
The manufacturing process proceeds with the molding phase, wherein the raw cast iron is shaped into brake drums using advanced casting techniques. Sand casting is predominantly employed due to its versatility and cost-effectiveness for large-scale production. This process involves creating a mold cavity from a sand mixture, into which molten cast iron is poured. Precision in mold design guarantees the fidelity of the brake drum’s final dimensions and features. It’s crucial for manufacturers to maintain tight control over the casting parameters, as inconsistencies can lead to defects such as porosity or uneven thickness, which can compromise the drum's reliability.
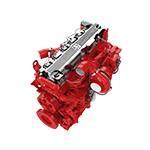
Following the casting, the brake drums undergo machining processes to achieve the definitive geometry and smooth finish necessary for performance. Turning, drilling, and milling operations are executed using computer numerical control (CNC) machines to ensure high precision and repeatability. Key operations include the machining of the mounting surfaces and bore, ensuring they meet strict dimensional tolerances. This stage is critical, as even minor deviations can affect the drum's balance and concentricity, leading to issues such as vibration or noise when installed in a vehicle.
brake drum manufacturing process
Quality control is integral throughout the entire manufacturing process. Each brake drum is subject to extensive inspection using state-of-the-art testing equipment. Non-destructive testing techniques like ultrasonic testing and magnetic particle inspection are employed to identify any subsurface defects. Additionally, sample drums are subjected to rigorous performance testing to simulate real-world braking conditions. These tests evaluate parameters such as friction coefficient, thermal performance, and structural integrity, ensuring each drum meets industry safety standards.
The incorporation of technological advancements has significantly augmented the brake drum manufacturing landscape. The advent of automation and the integration of Industry 4.0 principles have led to enhanced production efficiencies and reduced human error. Real-time data monitoring and analytics allow for predictive maintenance and process optimization, ensuring consistent product quality. Furthermore, the development of environmentally friendly materials and processes highlights the industry’s shift toward sustainability, reducing the environmental footprint of brake drum production.
To excel in the competitive global market, manufacturers must continuously innovate and adapt to evolving technological trends. Collaboration with automotive experts and participation in international standard-setting bodies contribute to the enhancement of expertise and authoritative knowledge in this domain. Establishing robust partnerships with suppliers and leveraging cutting-edge research are vital to maintaining leadership and trustworthiness in brake drum manufacturing.
In conclusion, the brake drum manufacturing process exemplifies the fusion of engineering excellence, quality commitment, and technological innovation. It is a field characterized by constant evolution, driven by the demands for performance, safety, and sustainability. Through meticulous processes and adherence to best practices, manufacturers ensure that brake drums not only meet but exceed the stringent requirements of modern automotive braking systems, affirming their indispensable role in vehicle safety.