In the realm of commercial vehicles, the bus brake drum stands as a cornerstone of safety and reliability. Understanding this vital component transcends mere mechanics; it intertwines expertise, experience, and trustworthiness to ensure vehicles stop efficiently, protecting both passengers and goods.

Bus brake drums are the unsung heroes of the road, tasked with the critical job of slowing down and stopping large, heavy vehicles. These drums are durable mechanisms made from advanced metal composites, specifically designed to withstand tremendous friction and heat. A typical brake drum works by receiving pressure from brake shoes, creating friction which slows the vehicle.
But not all brake drums are created equal; quality varies significantly across manufacturers.
Investing in high-quality bus brake drums is non-negotiable for fleet owners and operators. Experience shows that premium brake drums, often forged from superior cast iron with high graphite content, offer enhanced wear resistance and heat dissipation capabilities. These features translate into longer life spans, minimizing the frequency of replacements and maintenance expenses. Additionally, the right brake drum not only ensures safety but also boosts the performance of the braking system, resulting in shorter stopping distances which can be crucial in emergencies.
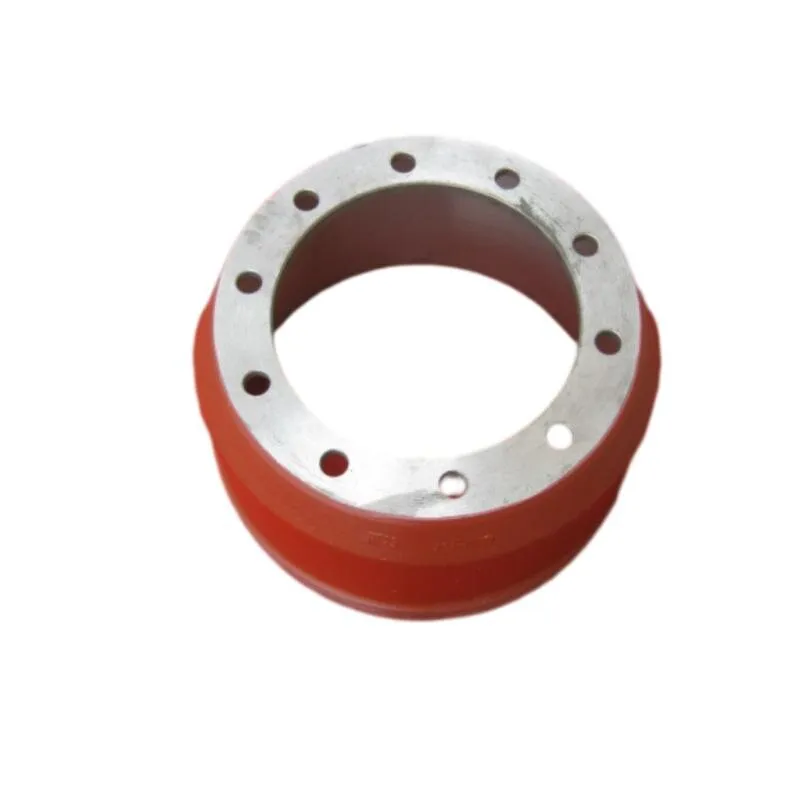
Professional expertise is essential when selecting the appropriate brake drum for specific bus models. It requires a deep understanding of the various specifications that affect compatibility and performance, such as diameter, width, weight, and bolt configuration. Engaging with an expert or trusted manufacturer can guide this choice, ensuring that the brake drums meet the specific needs of the vehicle and comply with safety regulations. This ensures operational continuity and enhances the overall efficiency of transportation services.
bus brake drum
Authoritativeness plays a pivotal role, especially when assessing different brands and models of brake drums available in the market. Experienced manufacturers with a strong industry reputation tend to guarantee product integrity. They often incorporate rigorous testing protocols to ensure that their products can withstand real-world conditions. Certifications from recognized automotive standards organizations are a hallmark of such reputable firms, signifying adherence to industry best practices and legal compliance.
Trustworthiness is cemented through transparency and accountability. A credible supplier provides clear information about the materials, manufacturing processes, and performance metrics of their brake drums. Offering warranties or guarantees also signals reliability, providing buyers confidence that they are investing in a product that the manufacturer stands behind.
It’s equally vital to consider the impact of maintenance on the lifespan and efficiency of brake drums. Regular inspections conducted by trained professionals can detect early signs of wear or damage, such as cracking, scoring, or abnormal wear patterns. Proactive maintenance not only extends the life of the brake drums but also assures the safety and reliability of the bus fleet.
In conclusion, choosing and maintaining bus brake drums requires a harmonious blend of experience, expertise, authority, and trustworthiness. It involves selecting high-quality products from reputable manufacturers, understanding the technical specifications tailored to individual bus models, and committing to regular maintenance practices. Through these measures, fleet operators can safeguard their investment, ensure passenger safety, and optimize operational efficiency.