Heavy truck brake drums are critical components in the transportation industry, ensuring the safe and efficient functioning of heavy-duty vehicles. Understanding their significance, construction, and maintenance can greatly enhance the performance and longevity of trucking fleets.
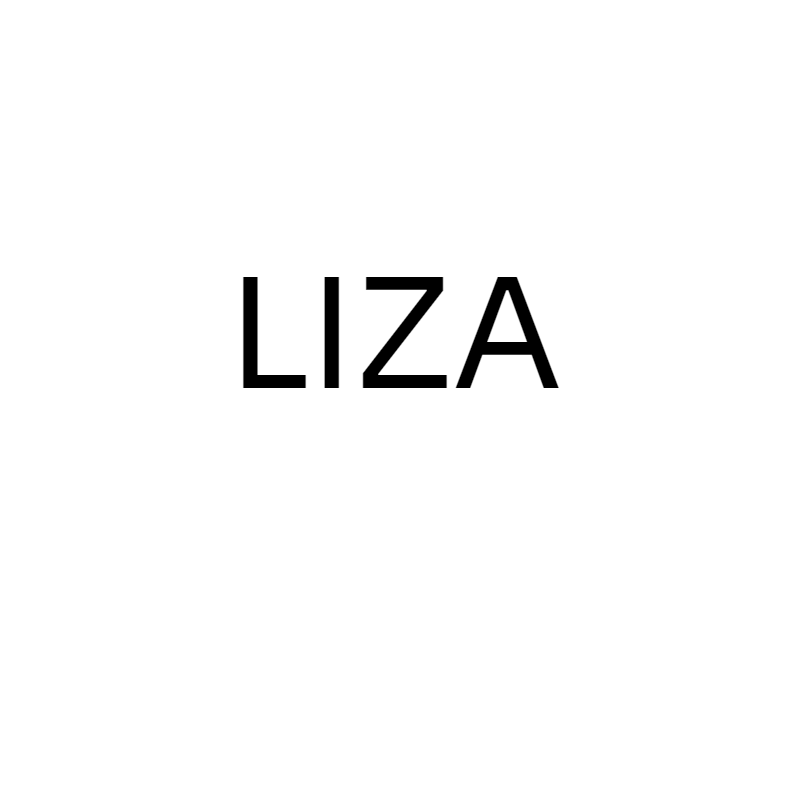
Brake drums for heavy trucks are engineered with precision to convert kinetic energy into thermal energy through friction. This process is paramount in decelerating or stopping a vehicle under load, making the strength and design of these drums vital. Typically constructed from cast iron due to its capacity to endure heat and wear, brake drums need to be exceptionally durable to withstand the demanding conditions of frequent stopping and high-speed braking.
Experience in the heavy truck sector underlines the fact that not all brake drums are created equal. Different brands and models offer varying levels of performance, based on factors such as the quality of materials used, manufacturing precision, and design enhancements. Experienced fleet operators often emphasize the importance of selecting brake drums that are specifically designed for their truck model to ensure compatibility and peak performance.
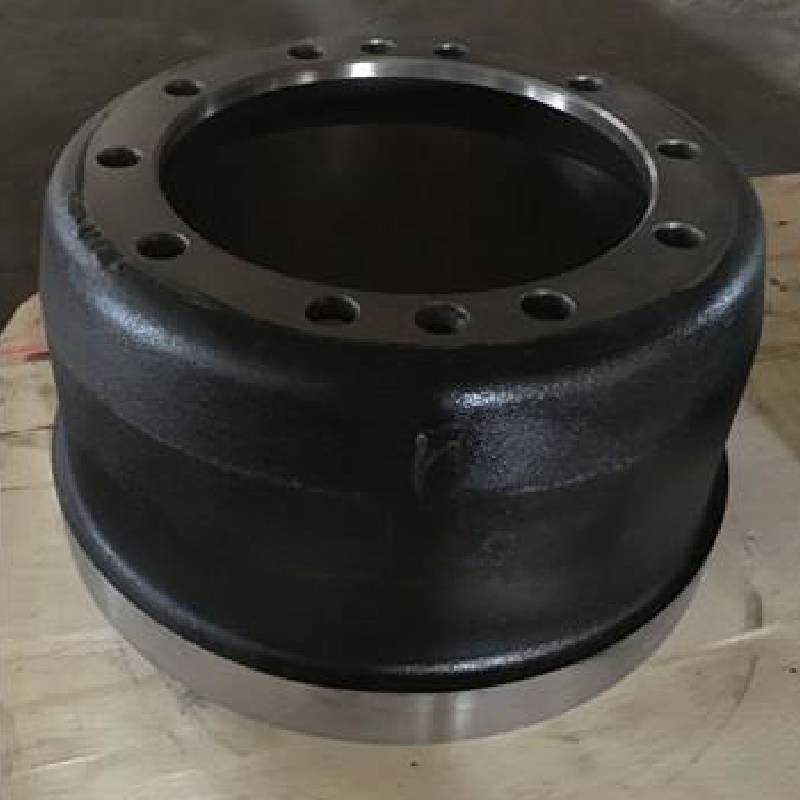
From a technical expertise standpoint, the diameter and thickness of a brake drum affect not only heat dissipation but also the overall braking performance. Thicker drums can provide better heat management but may contribute to more unsprung weight, which affects fuel efficiency. Thus, finding the right balance is essential for optimizing both braking safety and operational economy.
heavy truck brake drums
Quality standards, such as those set by the Society of Automotive Engineers (SAE) and the Department of Transportation (DOT), provide authoritative guidelines on the performance and safety of heavy truck brake drums. These standards are designed to ensure that drums can handle specified loads and environmental conditions, offering a benchmark for manufacturers and a reference for fleet operators.
Trustworthiness in brake drum manufacturing is often signaled by certifications and compliance with industry standards. The reliability of these components is backed by rigorous testing procedures, including fatigue tests, thermal cycling, and real-world endurance trials. Employing brake drums that meet these stringent standards minimizes the risk of brake failure and enhances safety.
Real-world application and environment greatly affect the longevity and effectiveness of brake drums. Factors such as terrain, load weight, and driving habits significantly influence wear patterns. For instance, trucks operating in mountainous regions or carrying heavy loads may experience more frequent replacements due to increased strain on braking systems. Consequently, establishing a routine maintenance schedule is critical. Regular inspections, ensuring proper lubrication of components, and replacing brake linings when necessary can prevent premature drum wear.
In conclusion, investing in high-quality brake drums tailored to specific truck models and operational needs can yield significant safety and economic benefits. Understanding the complexities of brake drum materials, design, and performance specifications allows fleet operators to make informed decisions that enhance operational efficiency. By prioritizing quality and adhering to the standards set by industry authorities, fleet managers can ensure the optimal performance and safety of their heavy-duty vehicles.