The brake drum, a critical component of a vehicle's braking system, plays an indispensable role in ensuring automotive safety and performance. Understanding its mechanism offers invaluable insights into automotive technology and underscores the importance of regular maintenance to ensure longevity and reliability.
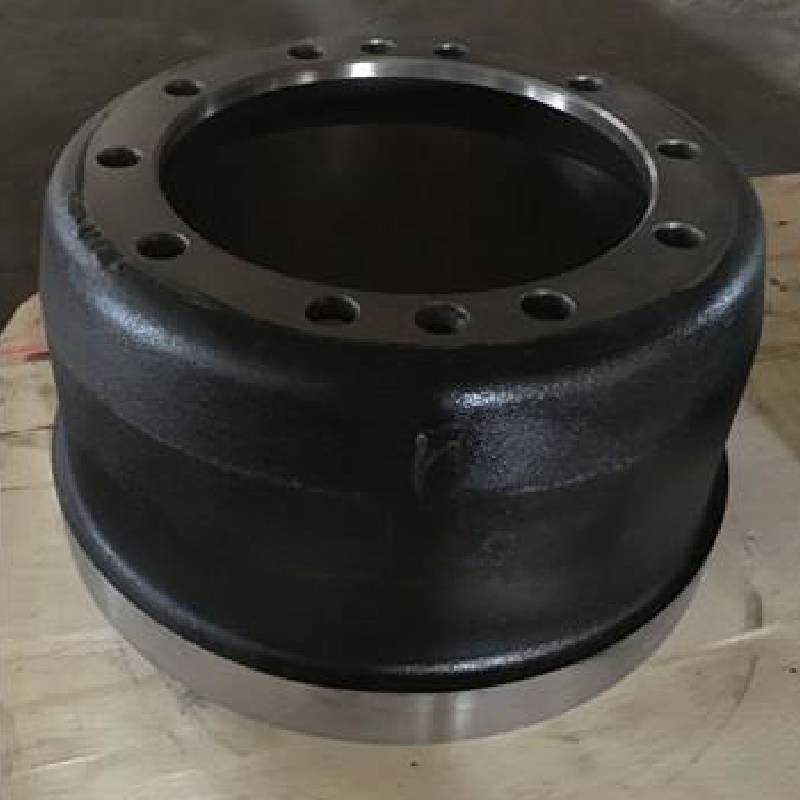
At the core of its function, the brake drum serves as the surface against which brake shoes exert pressure. When the brake pedal is engaged, hydraulic fluid pressure is transmitted through the brake lines, forcing the brake shoes outward against the inner surface of the drum. This frictional contact slows down vehicle rotation and ultimately brings the vehicle to a halt. The material composition of the drum, typically cast iron, is carefully chosen to withstand high frictional heat and resistance, which underscores its durability and effectiveness in diverse conditions.
Experts in the automotive field often emphasize the importance of understanding how brake drum systems interact with other braking components. Unlike disc brakes that have calipers to exert force, drum brakes rely on wheel cylinders to push brake shoes against the drum surface. This difference significantly affects braking efficiency, as well-designed drum systems can offer superior stopping power and heat dissipation in certain vehicle types, particularly larger, heavier vehicles like trucks and buses.
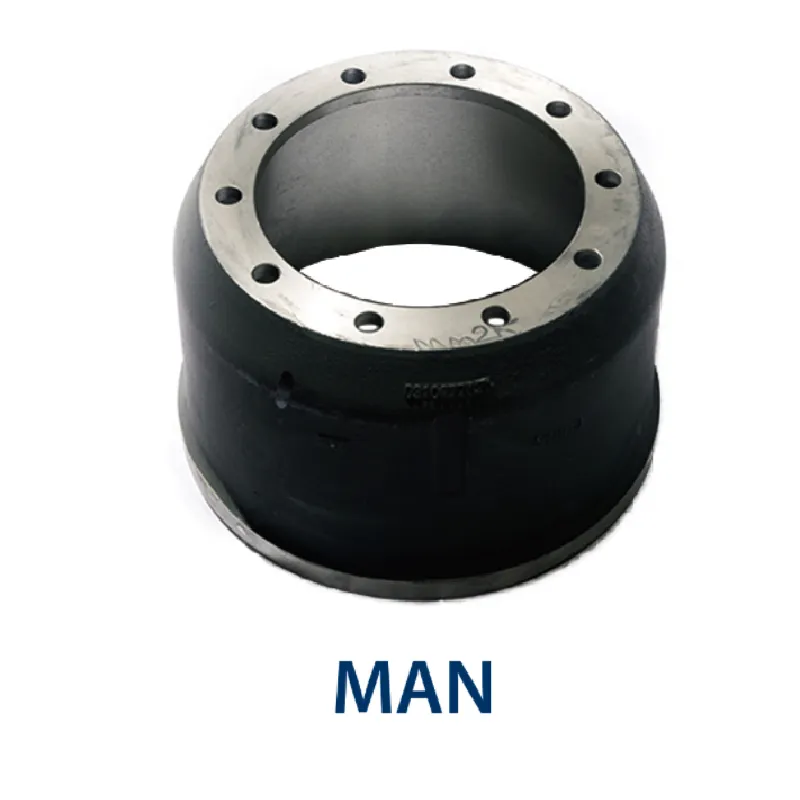
From an experiential standpoint, drivers and maintenance personnel often report that brake drums, while cheaper than disc brakes to maintain, require more frequent inspection to assess wear and tear on the drum surface and the brake shoes. Worn-out shoes can significantly impact braking performance, leading to increased stopping distances and potential safety hazards.
Over time, brake drums can develop a range of issues such as scoring, out-of-roundness, and heat cracks. These problems often arise from prolonged use without proper maintenance. Scoring is typically a result of excessive friction, leading to uneven wear on the drum's surface. Out-of-roundness occurs when a drum loses its perfectly circular shape, causing vibrations during braking. Heat cracks are due to rapid cooling and heating cycles that the drums endure. Such issues highlight the necessity for routine inspections by qualified professionals who can identify potential problems before they become serious.
how does a brake drum work
When selecting replacement brake drums, it’s crucial to consider the manufacturer’s reputation and product specifications. High-quality brake drums are precisely machined to fine tolerances, which ensures smooth, consistent performance and long-lasting reliability. Trusted manufacturers often provide detailed installation instructions and offer customer support to address any challenges faced during installation or use.
Additionally, environmental conditions play a significant role in how brake drums perform over time. In areas with high humidity or road salt usage, corrosion can compromise the drum's integrity. Regular cleaning and application of corrosion-resistant coatings can prevent deterioration and maintain optimal function.
Safety remains the paramount concern when discussing the mechanics of brake drums. Professionals urge vehicle owners to heed any warning signs such as squealing noises, vibrations, or decreased responsiveness when applying brakes, as these symptoms often indicate underlying issues with the brake drum system that require immediate attention.
In conclusion, the brake drum is an engineering marvel that showcases the intricate balance between mechanical design and material science. Its significance in vehicle safety cannot be overstated, making it imperative for vehicle owners and automotive professionals alike to prioritize regular maintenance and opt for quality components. As with any critical vehicle component, a proactive approach to care and expertise can ensure that brake drums perform seamlessly, providing peace of mind and safety for drivers and passengers.