Hub pilot brake drums play a crucial role in the efficiency and safety of commercial vehicles' braking systems. As an essential component of the motor vehicle industry, they demand precision engineering and rigorous quality standards to ensure optimal performance. When discussing the details surrounding hub pilot brake drums, it is important to focus on the real-world experiences and expert insights that underline their significance.
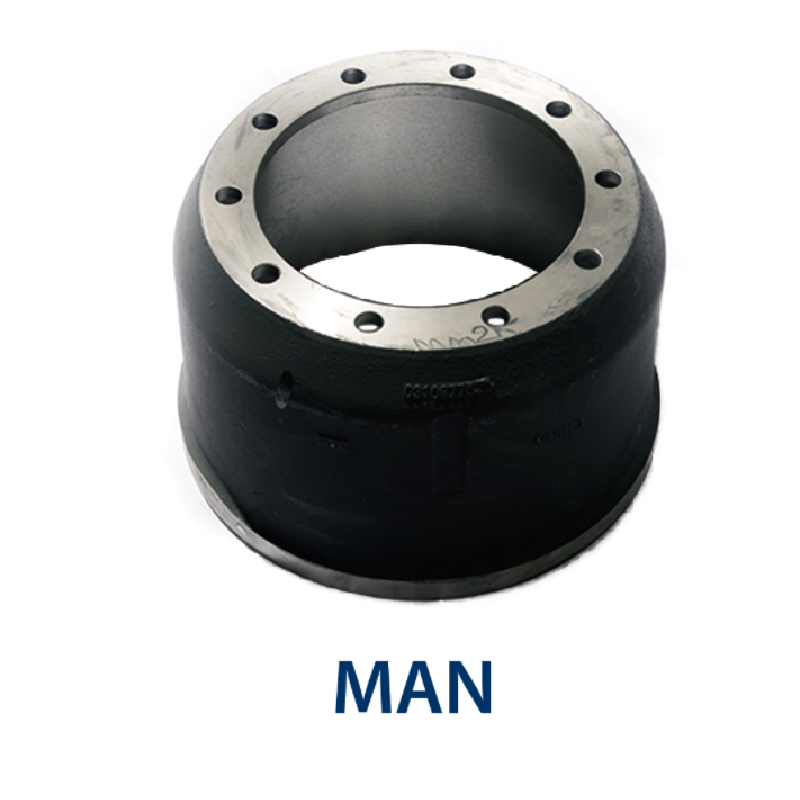
Brake drums encompass the core of the braking system, translating hydraulic pressure into mechanical force to facilitate vehicle deceleration. The hub pilot design specifically refers to how the brake drum centers itself on the hub using the central hub portion, rather than the studs. This design principle is fundamental for large commercial vehicles as it enhances consistency in wheel alignment and load distribution.
One prominent experience among fleet operators is the tangible improvement in fuel efficiency and reduced wear-and-tear on tires and suspension systems attributed to using hub pilot systems. This is primarily because the hub pilot arrangement prevents concentricity issues that might arise with lug-centric systems, where the wheel's alignment relies on the studs, potentially leading to uneven weight distribution and increased component wear.
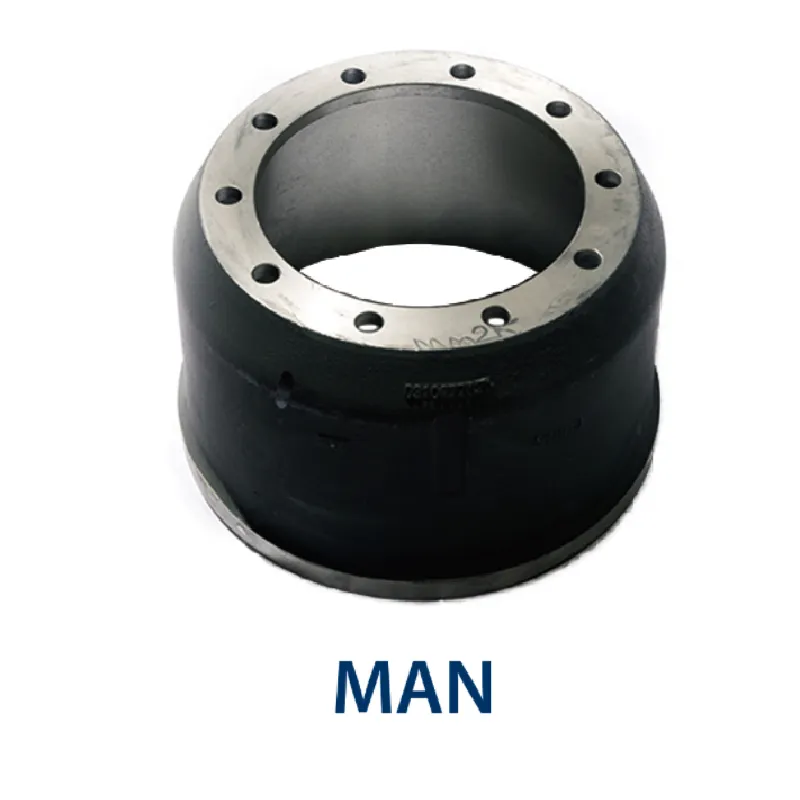
From an expert's perspective, selecting high-quality hub pilot brake drums involves a few key considerations. First,
the composition of the drum material is essential. Typically, these brake drums are made from gray iron due to its excellent wear resistance and dissipative properties. However, manufacturers must maintain stringent quality control during the casting process to ensure uniformity and the elimination of defects that could compromise the drum's structural integrity.
hub pilot brake drums
Moreover, precision machining is of paramount importance. The machined surfaces must maintain exacting tolerances to ensure a proper fit and function. This level of detail is critical, as any deviation can affect braking performance, leading to vibrations, noise, or even brake failures, posing severe safety risks.
The authoritative aspect of hub pilot brake drums is reinforced through their adherence to industry standards. Compliance with standards such as those set by the Society of Automotive Engineers (SAE) and the International Organization for Standardization (ISO) offers assurance of quality and compatibility across different vehicle systems. Brake drums that meet these standards guarantee interoperability and reliability, essential points for fleet maintenance and safety compliance.
In exploring trustworthy sources, partnerships with established manufacturers who have a track record of responsible production and innovation are vital. Renowned manufacturers invest in research and development to improve brake drum technology continually. They provide detailed certifications and testing results, which can be indispensable for fleet managers seeking reliable and high-performing components.
In conclusion, hub pilot brake drums are not merely a component; they are a pivotal part of vehicle safety and operational efficiency. By integrating real-world experiences, leaning on industry expertise, and adhering to authoritative standards, fleet operators can ensure their equipment's reliability and longevity. Trustworthiness is augmented by choosing partners with a proven history in producing high-quality brake components, thereby enhancing both vehicle performance and safety on the road.