Efficiently removing a Nissan forklift brake drum is critical for maintaining optimal performance and ensuring worker safety in material handling environments. Mastery of this process requires a blend of experience, technical knowledge, and adherence to safety protocols, reflecting the principles of Experience, Expertise, Authoritativeness, and Trustworthiness.
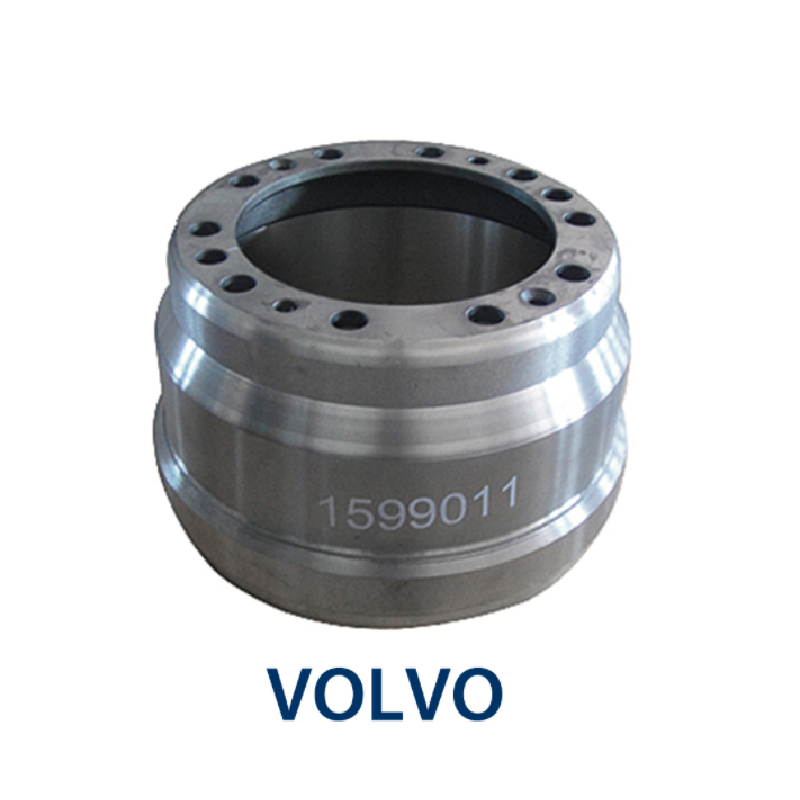
Firstly, understanding the mechanism of a forklift brake drum enhances one's ability to approach the task confidently. The brake drum is integral to the wheel assembly, facilitating the deceleration and halting of the vehicle through friction. Recognizing its essential role underscores why proper maintenance is non-negotiable.
Preparation is crucial. Position the forklift in a safe, level work area and secure it using wheel chocks and safety stands. Disconnect the battery to eliminate any risk of accidental activation. Wearing appropriate personal protective equipment (PPE) is imperative to ensure personal safety against possible injuries during this mechanical operation.
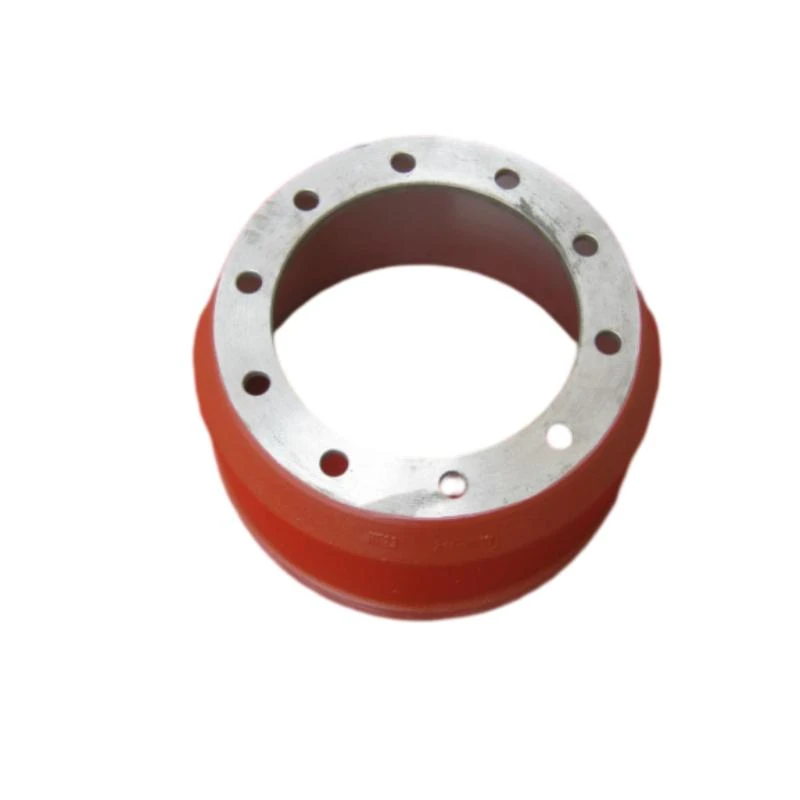
Experience shines when the nuances of removing a brake drum become second nature. Begin by removing the wheel assembly, which may vary slightly depending on the Nissan model. This typically involves loosening the lug nuts and carefully sliding the wheel off the hub, ensuring no components are damaged in the process.
With the wheel removed,
the brake drum becomes accessible. Expertise dictates an initial inspection for any visible rust, dirt, or debris that might hinder smooth removal. In some cases, the brake drum may be stubborn due to corrosion or tight contact with brake shoes. Gently tap around the drum's surface with a rubber mallet, ensuring distributed impact to free the drum without causing deformation.
An authoritative approach involves referring to the specific Nissan forklift model manual for precise guidance. These manuals often contain detailed schematics and torque settings, which are invaluable for maintaining the equipment’s integrity post-service. They empower technicians to adhere strictly to manufacturer specifications, avoiding generic solutions that might compromise the system.
nissan forklift brake drum removal
Professionals often encounter challenges like seized brake drums. In such instances, the application of a penetrating oil can be advantageous. Allow the oil to penetrate for several minutes before another gentle attempt at removal. Employing a drum puller can also aid in detaching the drum effectively, reflecting a deep understanding of problem-solving techniques in mechanical contexts.
Sound knowledge of the drum components is paramount for a successful operation. Identifying any worn or damaged parts during removal is a sign of expertise and contributes to longer life and better performance of the rollers. When the drum resists removal due to excessive wear or lip catching the shoe, a trustworthy mechanic carefully retracks the brake adjuster through an access hole at the backplate. This skill not only helps in removing the drum effortlessly but also minimizes the risk of damaging other connected parts.
Post-removal, a thorough inspection of the brake mechanism is mandatory. This inspection should extend to the brake shoes, adjuster, and other components to determine their condition and if replacement is required. Maintaining a keen eye for wear and deterioration is where trust in a technician’s skill mirrors experience and knowledge.
Reinstallation is just as critical as removal, demanding attention to detail. After cleaning and, if needed, replacing the brake parts, reinstall the drum carefully. Avoid any forceful methods that might skew the alignment or damage new components. The wheel assembly follows, and each lug nut must be torqued to specification, reflecting precision and professionalism.
In conclusion, the removal of a Nissan forklift brake drum demands a synergy of seasoned experience and technical expertise. Safety, and the longevity of the equipment, hinge on performing these tasks with authority and trustworthiness. This commitment to high standards ensures handling operations remain safe and effective, ultimately enhancing operational efficiency in industrial settings.