Understanding the nuances of automotive components is crucial for any vehicle enthusiast or professional mechanic, especially when it comes to vital parts like the 12 brake drum. Brake drums are an integral component of drum brake systems, often found in older vehicles and some light trucks today. Their function is essential for safety and performance, making expertise in this area valuable.
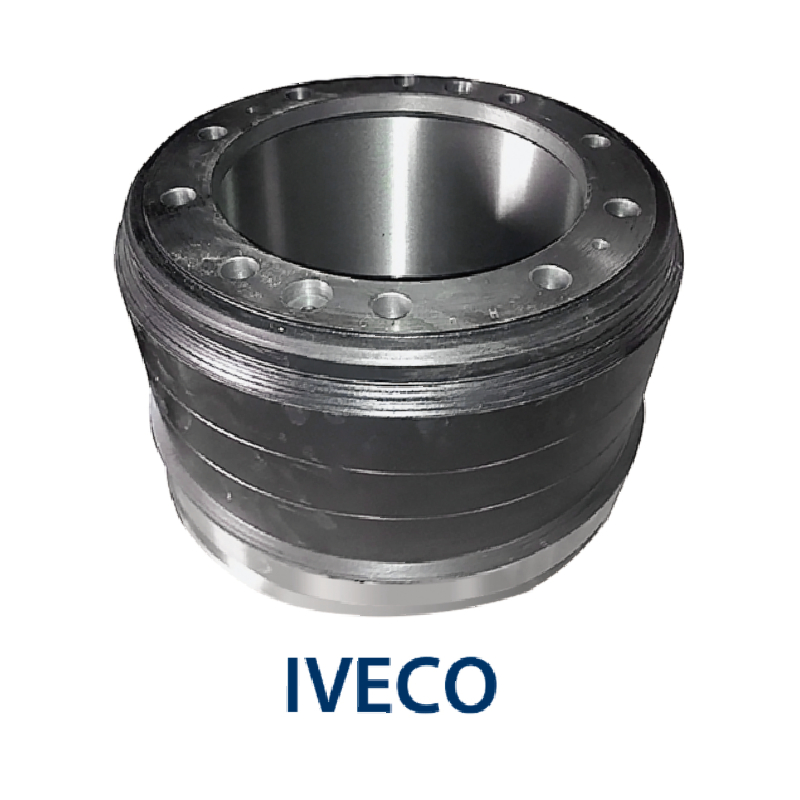
The 12 brake drum refers to a drum with a diameter of 12 inches, commonly used in various heavy-duty vehicles. The performance and longevity of brake drums depend heavily on material quality and maintenance practices. Typically, these drums are made from cast iron due to its excellent wear resistance and ability to dissipate heat efficiently. Balancing quality and cost, cast iron is preferred for its longevity and reliability under frequent braking conditions.
From a technical perspective, the 12 brake drum works in conjunction with brake shoes and wheel cylinders. When the brake pedal is pressed, hydraulic pressure forces the brake shoes outward against the internal surface of the drum, creating friction that slows down the wheel's rotation. This system relies heavily on the precise engagement between the drum and shoe, emphasizing the need for precision in the drum’s manufacturing and maintenance.
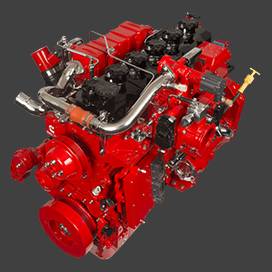
Expertise in brake drum maintenance is critical. Regular inspection is required, especially in vehicles subjected to heavy loads or frequent stop-and-go traffic, as these conditions exacerbate wear and overheating. Signs of wear include grooves on the drum surface or diminished braking performance, often manifesting as longer stopping distances or a spongy brake pedal.
12 brake drum
Replacing a 12 brake drum should only be done with precision. First, ensure compatibility with the vehicle's make and model to avoid operational inefficiencies or safety risks. Proper installation requires uniform torque application on mounting bolts and adherence to manufacturer specifications to prevent issues like warping or vibration, which can significantly undermine braking performance.
Choosing high-quality replacement drums is also crucial. Brands that offer precision-machined surfaces, excellent balance, and heat-treated iron can enhance performance and extend the drum’s lifespan. Trustworthy manufacturers often provide detailed product information and specifications, ensuring transparency and reliability for consumers. When possible, consult experienced professionals who can provide insights into the best products and practices based on firsthand experience and extensive technical knowledge.
Consistency in brake system maintenance cultivates trustworthiness and expertise. Professionals recommend a routine check at intervals aligned with the manufacturer’s guidelines, or sooner if the vehicle is exposed to harsh driving conditions. During maintenance, technicians not only inspect the drum but also evaluate accompanying components such as shoes, wheel cylinders, and springs for wear and corrosion.
Ultimately, the 12 brake drum is a vital component whose role cannot be overstated. Understanding its function, recognizing the signs of wear, and applying expert maintenance practices ensures optimal performance and safety. Through informed choices and regular professional consultation, both vehicle owners and mechanics can guarantee that this critical component functions efficiently, safeguarding the integrity of the entire braking system.