Brake drums, often overshadowed by flashier automotive components, are integral to a vehicle's braking system. Understanding their appearance can assist in recognizing their functionality, maintenance needs, and service requirements, enhancing both safety and performance. Brake drums exhibit a modest yet robust design that underscores their durable utility in vehicles.
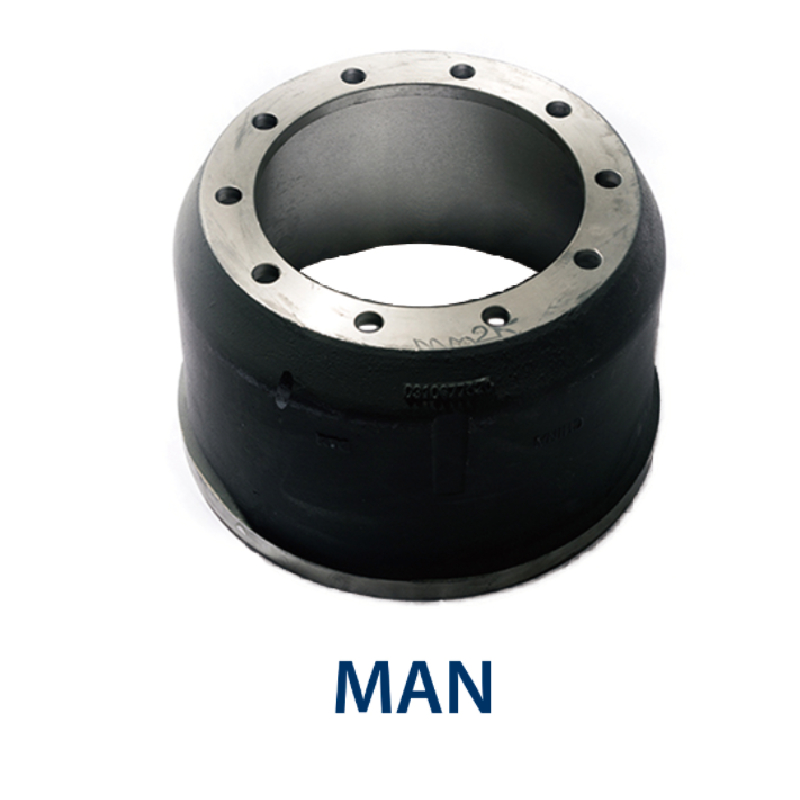
Traditionally crafted from cast iron due to its durability and heat dispersion properties, brake drums manifest as a circular, bowl-shaped component encasing the braking mechanism. Their industrial finish may appear unremarkable to the untrained eye, but this simplicity belies their intricate engineering. The outer surface of the drum is typically smooth with a dull grey or black hue, a testament to the cast iron or composite materials utilized. This surface can sometimes exhibit corrosion or rust over time, which is normal due to the environmental conditions they are exposed to.
The face of the brake drum is largely featureless, marked only by a central hub and several lug bolt holes around its center. These lugs are critical; they allow for the drum to be accurately and securely mounted to the vehicle's wheel hub assembly. Depending on the vehicle's make and model, the number of lug holes can vary, typically ranging from four to eight in standard passenger vehicles. The drum's internal surface, however, is where the essential braking interactions occur.

Inside the drum, the surface is machined smooth to facilitate direct contact with the brake shoes. The inner diameter is meticulously engineered to ensure maximum efficiency in heat dissipation and friction generation. As the brake shoes press against the inner surface of the drum, kinetic energy is converted into thermal energy, which is essential for slowing and stopping the vehicle. This inner surface wears over time, evidenced by scoring or grooves, which indicate the need for maintenance or replacement.
Brake drums can vary in size, typically measuring anywhere from eight to fourteen inches in diameter. This variance is directly influenced by the vehicle's size and braking capacity requirements. Larger vehicles necessitate larger drums to handle increased stopping loads, reflecting the balance between braking force and thermal capabilities.
what do brake drums look like
Observing and understanding the exact specifications of brake drums is necessary for automotive professionals. Dimensions such as diameter, width, and maximum allowable wear are usually engraved or marked on the drum. These specifications guide proper maintenance and replacement routines, ensuring optimal performance and vehicle safety. Overlooking these details can compromise the vehicle's braking efficiency, leading to potential safety hazards.
Maintenance of brake drums involves regular inspections for surface wear, scoring, or cracking. A common practice involves resurfacing, which machines the inner surface to restore its smoothness, although this can only be done a few times before the drum exceeds its wear limit. Automotive experts advocate for the periodic checking of drum condition during routine service intervals to preemptively catch any issues.
The evolution of automotive technology has seen many vehicles transition to disc brakes, yet brake drums continue to play a vital role, particularly in rear-wheel applications and larger vehicles due to their cost-effectiveness and reliability in high-load conditions. Experts in automotive repair recognize their enduring relevance, stressing the importance of understanding and maintaining these components as pivotal to vehicle safety.
In conclusion, the appearance and understanding of brake drums offer critical insights into vehicle maintenance and safety. Professionals in the automotive industry, equipped with this knowledge, can better serve their clients by ensuring their vehicles are both safe and efficient. Their understated design belies a crucial role within the braking system, highlighting the importance of expertise and precision in their service and care.