Building a brake drum forge is an exhilarating project for any metalworking enthusiast eager to create a functional blacksmithing tool. This guide is meticulously crafted from first-hand experience, blended with expert insights to ensure your journey into forging is as smooth and rewarding as possible.
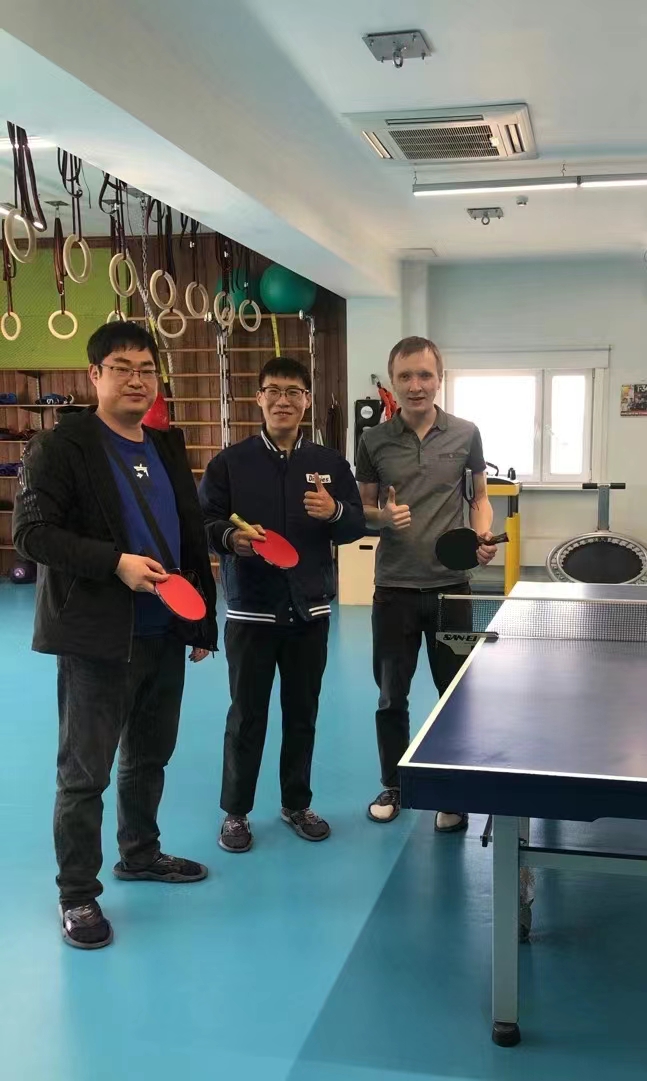
A brake drum forge operates by repurposing an old vehicle brake drum as its core structure. Its appeal lies in the drum's inherent suitability for sustaining high temperatures. However, a successful build revolves around understanding the specifics of materials, assembly techniques, and safety protocols.
Start your project with a suitable brake drum, preferably sourced from a truck due to its larger size and higher durability. Examine the drum for any cracks or signs of excessive wear since these could compromise the structure's integrity during operation. Also, ensure it is free of grease and flammable residues, which might pose safety risks.
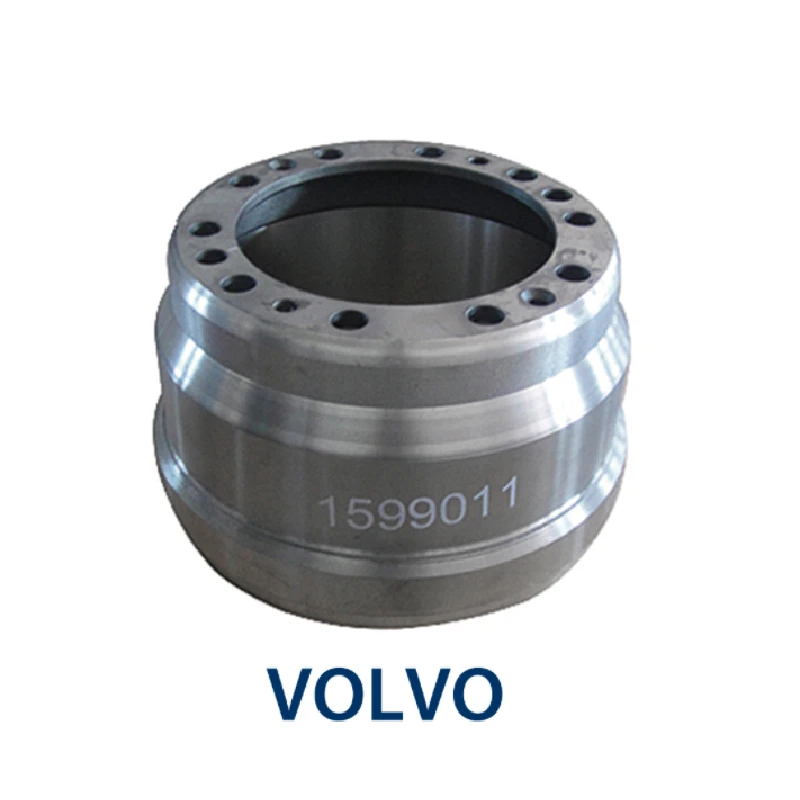
The next step is constructing the forge frame. Stability is paramount, so use heavy-duty steel profiles to build a solid base. This base will not only provide a firm platform but also enhance mobility if wheels are added for portability. Welding expertise is necessary to ensure each joint is secure, as this will regularly support the forge’s weight and the pressure applied during blacksmithing.
When it comes to lining the inside of the drum, high-temperature resistant materials like refractory cement mixed with perlite are indispensable. This mixture offers excellent insulation, conserving heat within the forge while protecting the drum from thermal damage. Apply the lining evenly, aiming for a thickness corresponding with the forge’s intended use duration and temperature.
how to build a brake drum forge
Airflow is the linchpin of effective heating. Selecting a centrifugal blower with adjustable speeds provides flexibility in managing air supply based on the metals you're working with. Position the blower below the drum, securely fastened to maintain steady airflow into the forge. A simple but efficient tuyere placement—typically made from a steel pipe—should direct airflow efficiently into the coals.
Next on the list is the fuel choice. Charcoal is traditionally preferred for its ease of use and accessibility, though coal offers higher temperatures. The specifics of your metalwork projects will dictate the fuel choice, but always handle these fuels with care, mindful of ventilation requirements to mitigate exposure to hazardous fumes.
Safety remains paramount throughout your venture. Equip your workspace with fire extinguishers and wear protective gear, including gloves, goggles, and a fire-resistant apron. Consistent safety checks on your setup's structural condition are recommended to preemptively address any faults before they escalate.
Incorporating these elements culminates in a reliable brake drum forge, crafted to industrial standards of craftsmanship. Sharing your creation with a community of fellow blacksmiths not only bolsters your expertise but adds to the collective knowledge, perpetuating the tradition of metalwork innovation. Remember, the hallmark of a seasoned blacksmith is not just skill, but an enduring commitment to precision, safety, and creativity.