The intricacies of the brake drum casting process play a crucial role in determining the performance and safety of the vehicles that rely on these essential components. Each brake drum must endure immense stress and friction over its lifespan, making its manufacturing process pivotal to ensuring safety and efficiency on the roads.
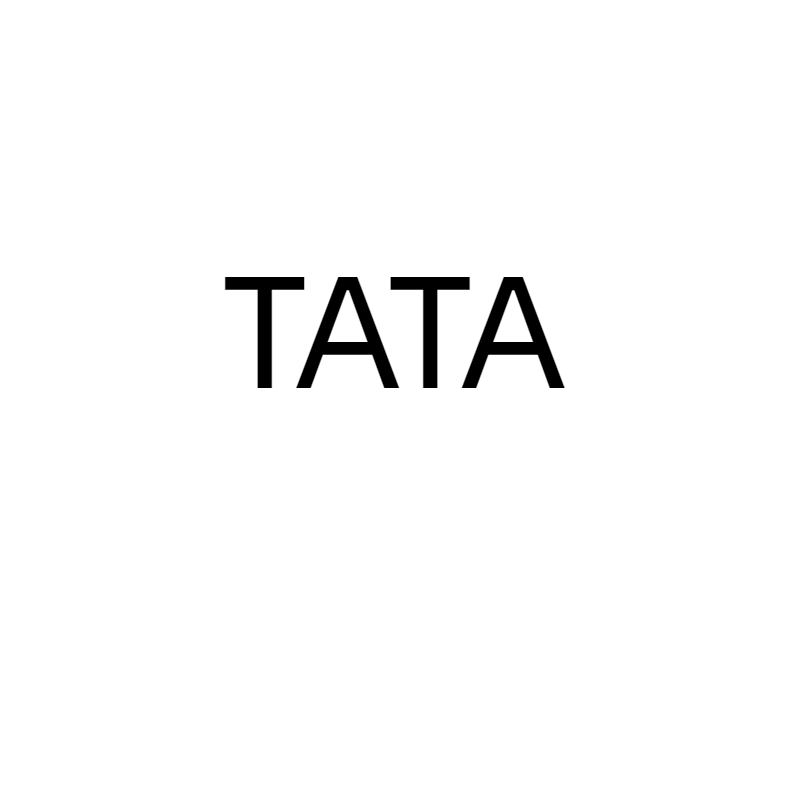
To develop a deeper understanding of the brake drum casting process, it's important to first recognize the manufacturing journey from raw material selection to final product testing. The journey begins with selecting the appropriate blend of metal alloys, often a grey iron known for its superior wear resistance and thermal conductivity. These materials are essential for the drum's ability to dissipate heat and withstand high-friction environments.
In the casting arena, expertise lies in the foundry’s ability to harness modern technology coupled with time-tested techniques. Molding, the first step in casting, uses a pattern of the brake drum, usually made of wood, plastic, or metal. Using sophisticated machinery, precision sand molds are formed around this pattern. The choice of sand and binding agent is critical, as it dictates the drum's surface finish and dimensional accuracy. It's here that computer-aided design (CAD) software demonstrates its authority by optimizing mold and pattern designs, thus reducing material waste and ensuring perfect symmetry.
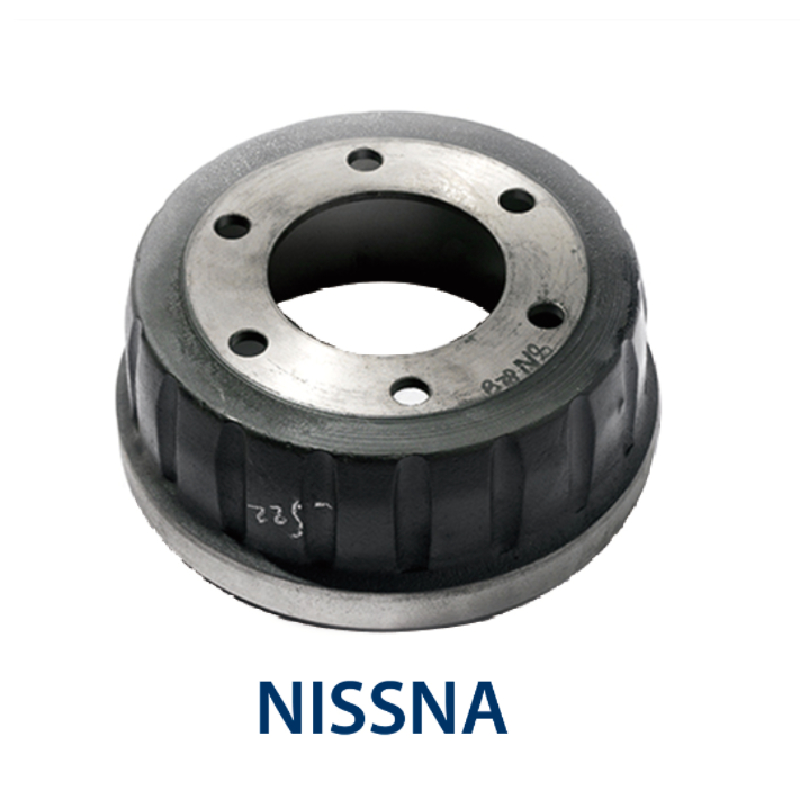
The melting process is where a foundry's expertise shines. Cast iron is melted in an induction furnace, maintaining a stringent focus on temperature control to preserve the integrity of the metal's microstructure. The molten metal is then carefully poured into the preformed sand molds. Ensuring minimal turbulence during pouring is crucial; experienced foundries master this delicate step to prevent inclusions and porosity, which can lead to structural weaknesses in the final product.
When discussing casting, one must not overlook the solidification phase. Here, trust in the foundry's control over cooling rates is paramount. By implementing controlled cooling systems, foundries mitigate internal stresses and enhance the mechanical properties of the brake drum. This step showcases both expertise and trustworthiness, as meticulous cooling ensures the durability and reliability of the product in real-world automotive conditions.
brake drum casting process
Once the casting has cooled and solidified, it's time for de-molding - the removal of the sand mold to expose the newly formed brake drum. This is followed by the fettling process, which involves removing any excess material or imperfections. High-quality castings undergo precise machining to meet exact specifications, an area where expert craftsmanship and authoritative precision come into play.
The final steps involve rigorous quality control inspections where each brake drum is examined for dimensional accuracy, balance, and surface finish quality. These inspections incorporate advanced non-destructive testing (NDT) methods to detect hidden defects. Only those drums meeting strict safety and performance standards are approved for distribution, reinforcing the trustworthiness of the manufacturing process.
The adoption of eco-friendly practices in the foundry cannot be understated. Many advanced foundries have integrated sustainability into their operations, from recycling used sand to implementing closed-loop waste management systems. These environmentally friendly practices not only elevate the company's standing as a responsible manufacturer but also ensure compliance with global environmental standards.
In essence, the brake drum casting process extends beyond mere production; it's an experiential journey underscored by authoritative precision and expert craftsmanship. Every phase, whether selecting the right alloy or ensuring the integrity of a cooling system, contributes to the overarching goal of safety, reliability, and environmental sustainability. Thus, for industry players seeking to elevate their positioning in the market through SEO, emphasizing these aspects of experience, expertise, authority, and trust can significantly enhance online visibility and consumer confidence in their products.
Through harnessing cutting-edge technology, environmentally responsible practices, and thorough quality assurance protocols, manufacturers can assert their authority and expertise in the ever-evolving automotive industry. It is this commitment to excellence in the brake drum casting process that ultimately reverberates through the performance and safety of countless vehicles worldwide.